From eccentric wheels to the counter-balanced “nodding donkey,” inventing ways to produce oil.
In a remote northwestern Pennsylvania valley on August 27, 1859, Edwin L. Drake completed America’s first commercial oil well — launching the U.S. petroleum industry. Drake borrowed a common kitchen hand-pump to retrieve the important new resource from a depth of 69.5 feet.
Seeking oil for the Seneca Oil Company for refining into a popular lamp fuel, kerosene, Drake’s shallow well created a new exploration and production industry, it wasn’t long before necessity and ingenuity combined to find something more efficient for producing oil from a well.
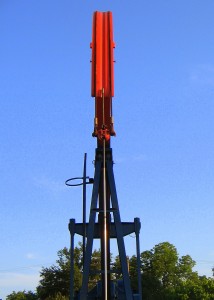
Invented in 1925 in Lufkin, Texas, the counterbalanced pumping unit brought greater efficiency to the oil patch. Photo by Bruce Wells.
As the nation’s new petroleum industry evolved, exploration and production pioneers realized improving oil well pump efficiency could greatly extend the economic life of far deeper wells.
By the time of the headline-making 1901 gusher at Spindletop Hill in Texas, pumping technology innovations were underway that would lead to the modern “nodding donkey.” These ubiquitous pumping units can be found at thousands of marginally producing oil wells reaching into both shallow and deep geologic formations.
Stripper Wells
Oil wells will run dry, but advances in “artificial lift systems” technology have helped put off the inevitable. Even with 21st century technologies, more than half of a producing formation’s oil can remain trapped underground.
Low-volume marginal or “stripper” wells produce less than 15 barrels a day, but the typical well produces less than three barrels per day. A marginal natural gas well does not exceed production of 90 thousand cubic feet of gas per day.
According to the National Stripper Well Association (NSWA), in 2020 there were an estimated 760,000 stripper wells in production, about 400,000 oil and 360,000 natural gas wells, and “that means, of one million active oil and natural gas wells in the United States, 76 percent are low production wells.”
For most marginal wells, once shutdown, they are lost forever.
Efficiently — and safely — producing oil and natural gas have long been a challenge for geologists and engineers. As wells have reached deeper, they have required new technologies combined with hard work in the field.
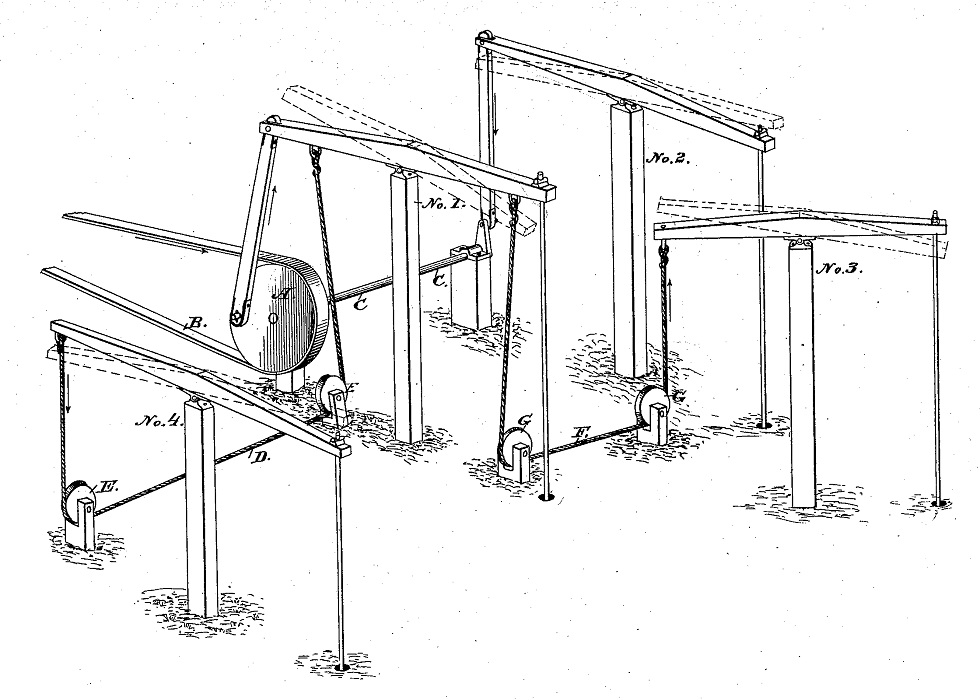
America’s oilfield technologies advanced in in the 1870s with patents like this “Improvement In Means For Pumping Wells,” invented in Pennsylvania.
“This is an occupation where most of your work is done in all types of weather while working alone, with few thanks, and possibly only a small herd of cattle as company,” noted Leslie Langston in the Oklahoma Marginal Well Commission’s The Lease Pumper’s Handbook in 2003.
It was the same in the industry’s earliest oil well pump days.
Central Power Units
Marginal quantities of oil always need help leaving the well. In the early days of the industry, oilmen adapted water-well technology to the problem and used steam-driven walking beam pump systems.
At each well, a steam engine rhythmically raised and lowered one end of a sturdy wooden beam, which pivoted on a Samson post. The walking beam’s other end cranked a long string of sucker-rods up and down to pump oil to the surface.
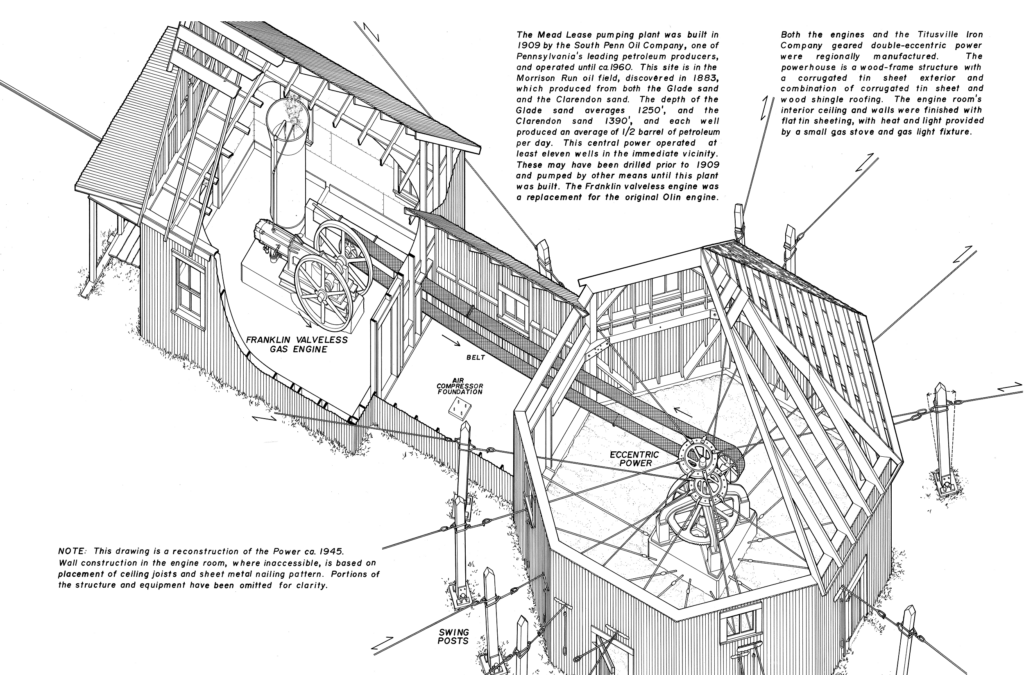
An oilfield “jack plant” often included a single-cylinder horizontal engine that rotated eccentric wheels. Details of a centralized plant built in 1909 by the South Penn Oil Company that operated in Warren County, Pennsylvania, until the 1960s, Image courtesy Library of Congress.
The beam walked and the oil surfaced, but a more efficient system was needed. One of the early oil pumping innovations came from an 1875 patent. An “Improvement in Means for Pumping Wells” allowed pumping of multiple wells with a single steam engine. The technology helped boost efficiency in the early oilfields of Venango County, Pennsylvania.
The new pumping method applied a system of linked and balanced walking beams to pump the oil wells. Wooden or iron rods instead of a rope and pulley system made the technology the forerunner of better production methods.
Learn more in Eccentric Wheels and Jerk Lines.
Walter Trout’s Revolutionary Prototype
As efficient as central power units were, time and technology changed the oilfield again. A new icon of U.S. petroleum production appeared and was soon known by many names: Donkey, Grasshopper, Horse-head, Thirsty Bird, and Pump Jack, among others.
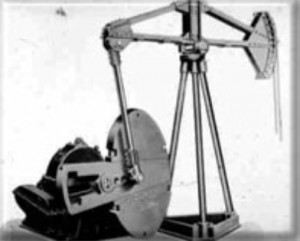
Sketched by Walter Trout in 1925, a prototype of his counterbalanced pump jack was in an oilfield before the end of the year.
As East Texas timber supplies dwindled and the sawmill business declined, the long-established Lufkin Foundry & Machine Company discovered new opportunities in the oilfield. As more oil discoveries arrived, the company — in Lufkin, Texas — not only survived, but prospered.
Walter Trout was working in Texas for Lufkin Foundry & Machine in 1925 when he sketched out his idea for the now familiar counterbalanced oil well pump jack.
Before the end of the year, the Trout prototype was installed and pumping oil at a well near Hull, Texas, in a Humble Oil Company oilfield.
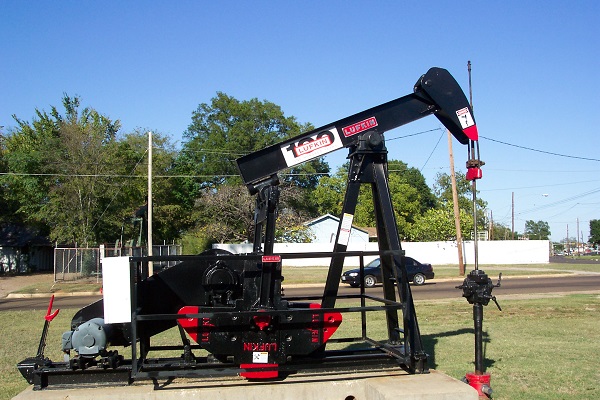
The founding of the Lufkin Foundry and Machine Company in 1902 would lead to creation of an oilfield icon known by many names — nodding donkey, grasshopper, horse-head, thirsty bird, etc. Photo by Bruce Wells.
“The well was perfectly balanced, but even with this result, it was such a funny looking, odd thing that it was subject to ridicule and criticism, and it took a long time, nearly a year, before we could convince many the idea was a good one,” Trout explained.
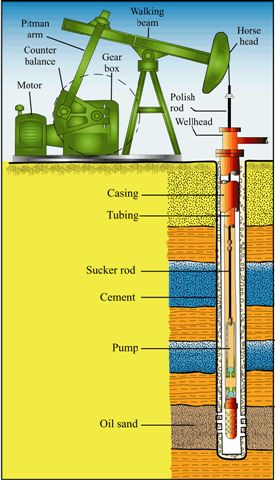
Key to pumping the oil (and often set to run on a timer), an engine turns gears that move a counter weight connected to the walking beam, which moves the sucker-rod up and down to up draw oil.
Ninety-nine years later, oilfield pumping units look much like Walter Trout’s original.
Although Lufkin Industries and other manufacturers continued to make them to meet worldwide demand, General Electric, which acquired Lufkin Industries for $3.3 billion in 2013, closed the downtown Lufkin foundry in 2015.
In addition pump jacks, electric submersible pump (ESP) systems also have become a vital artificial lift method of pumping production fluids (learn ESP history in Inventing the Electric Submersible Pump).
Smart Pumping Technology
As with nearly every segment of the petroleum industry, artificial lift systems — including the venerable pump jack — are also benefiting from inclusion of “smart” technology.
“The computer-based technology is used to monitor and analyze pump systems in real time from miles away, quickly and with minimal human interference,” explained Paul Nelson of Houston-based Weatherford International Ltd. in a 2001 article for Oil and Gas Online.
“On pump jacks that means constant monitoring of well production and the lift unit in order to optimize energy usage while maximizing the amount of oil recovered from reluctant zones,” Nelson added.
Smart well technology has become of particular importance to the United States, where a very large portion oil is produced from thousands of small stripper wells producing less than 10 barrels a day.
Many stripper wells have reached such a depleted pressure state that once they are shut in they can never be economically restarted. The majority of them must be kept alive by oil well pump jacks.
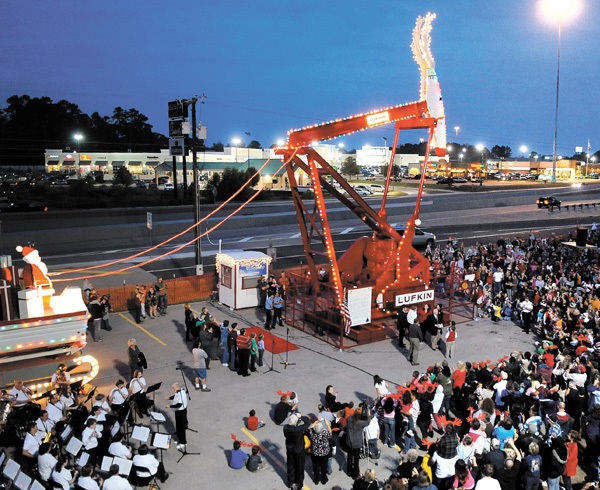
The lighting of “Rudolph the Red Nosed Pumping Unit” in 1966 became an annual event at Lufkin, Texas. More than 1,000 lights were added to a fully operational, 45-foot-tall pump jack. Photo courtesy the Lufkin Daily News.
“By improving pump efficiencies without adding significantly to operating costs, smart well technology stands to extend by years the economic life of many of these wells and, by extension, add millions of barrels of oil to U.S. reserves,” he concluded.
Reservoir Management
In October 1942, the East Texas Salt Water Disposal Company of Tyler drilled the first salt water injection well in the 12-year-old East Texas oilfield. As early as 1929, the Federal Bureau of Mines had determined injecting recovered saltwater into formations could increase reservoir pressures and oil production of the “Black Giant” oilfield.
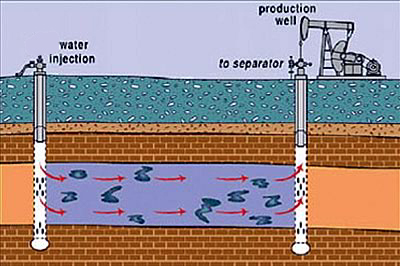
Saltwater injection wells improved oil production in the giant East Texas oilfield.
The Texas Railroad Commission established the salt water disposal company as a public utility to operate in the oilfield. The company treated and re-injected about 1.5 billion barrels of saltwater in its first 13 years, prompting one commissioner to proclaim saltwater injection as the “greatest oil conservation project in history.”
Drilling Technologies
Edwin L. Drake (1819-1880) became the “father of the petroleum industry” when he drilled what most consider America’s first commercial oil well on August 27, 1859, near Titusville, Pennsylvania. He used a steam engine and cable-tool rig.
Drake pioneered new drilling technologies, including using iron casing to isolate his well bore from nearby Oil Creek. Within days of his discovery, a competitor used a simple “spring pole” to drill the petroleum industry’s first dry hole.
Drilling technologies, including rotary “fishtail” bits and the first dual-coned bits of Howard Hughes Sr., are described in Making Hole — Drilling Technology. Another drilling advance came in 1933 with the use of slant drilling — see Technology and the “Conroe Crater.“
_______________________
Recommended Reading: Lufkin, from sawdust to oil: A history of Lufkin Industries, Inc. (1982); Modern oil-well pumping, An Oil and gas journal book (1962); Myth, Legend, Reality: Edwin Laurentine Drake and the Early Oil Industry
(2009). Your Amazon purchases benefit the American Oil & Gas Historical Society. As an Amazon Associate, AOGHS earns a commission from qualifying purchases.
_______________________
The American Oil & Gas Historical Society (AOGHS) preserves U.S. petroleum history. Please become an AOGHS annual supporter and help maintain this energy education website and expand historical research. For more information, contact bawells@aoghs.org. Copyright © 2024 Bruce A. Wells. All rights reserved.
Citation Information – Article Title: “All Pumped Up – Oilfield Technology.” Authors: B.A. Wells and K.L. Wells. Website Name: American Oil & Gas Historical Society. URL: https://aoghs.org/technology/oil-well-pump. Last Updated: April 14, 2024. Original Published Date: September 1, 2006.