by Bruce Wells | Jan 2, 2025 | Petroleum Technology
The ingenuity of a skilled machinist and a Texas wildcatter created a device to stop gushers.
Petroleum drilling and production technologies, among the most advanced of any industry, evolved as exploratory wells drilled deeper into highly pressurized geologic formations. One idea began with a sketch on the sawdust floor of a Texas machine shop.
In January 1922, James Abercrombie and Harry Cameron sought their first U.S. patent for the hydraulic ram-type blowout preventer (BOP). The invention would become a vital technology for ending dangerous oil and natural gas gushers. (more…)
by Bruce Wells | Dec 29, 2024 | Petroleum Technology
The petroleum industry’s difficult job of retrieving broken (and expensive) equipment obstructing an oil well — “fishing” — began in 1859 when a drilling tool stuck at 134 feet deep and ruined a Pennsylvania well. The technical challenges at far greater depths have tormented exploration companies ever since.
Just four days after the August 27, 1859, first U.S. oil discovery by Edwin L. Drake at Titusville, Pennsylvania, a much less known oil and natural gas industry pioneer began America’s second well to be drilled for petroleum. John Livingston Grandin dug his well nearby using a simple spring pole — but soon wedged his iron chisel downhole.
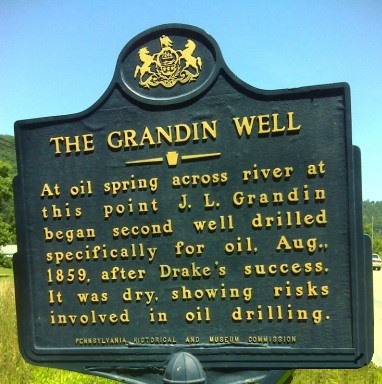
John L. Grandin attempted to recover a lost drill bit at his 1859 well near Tidioute, Pennsylvania. Warren County roadside marker photo.
The 22-year-old Grandin improvised his own well fishing tools, but not only lost his drill bit (an industry first), he ended up with America’s first dry hole among other petroleum industry milestones.

Searching for oil was less an earth science and more an art in the exploration and production industry’s earliest days. Geologists in Pennsylvania’s “valley that changed the world” knew far more about finding coal seams than characteristics of oil-bearing formations.
Making Hole
Even as drilling technologies evolved from spring poles and cable tools to modern rotary rigs, downhole problems remained — especially as wells reached new depths (learn more in Making Hole — Drilling Technology).
A 19th-century cable-tool rig, like its ancient predecessor the spring pole, utilized percussion drilling — the repeated lifting and dropping of a heavy chisel using hemp ropes. Drilling time and depth improved with the addition of steam power and tall, wooden derricks.
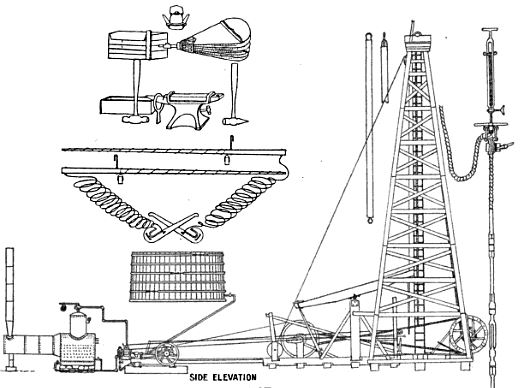
A standard, 82-foot cable-tool derrick used a steam boiler and one-cylinder engine connected to a “walking beam. Image from The Oil-Well Driller, 1905.
As depths increased, frequent stops were needed to bail out water and cuttings — and sharpen the bit’s iron edge. Small forges were often just feet from the well bore.
Despite drillers trying to avoid having expensive tools jammed deep in the well, accidents happened. The cable-tool rig’s manila rope or wire line would break. A pipe connection might bend. The downhole tool assemblies could no longer be lifted and dropped.
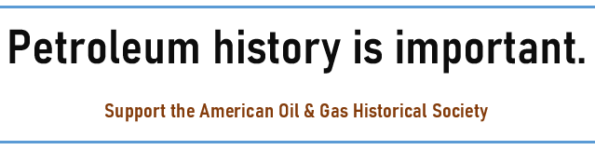
On the rig floor, fishing tools had to be lowered by a line into the well, armed at their end with spears, clamps and hooks. Sometimes a wood, wax and nails “impression block” was first lowered to get an idea of what lay downhole.
Hooks and Spears
In percussion drilling, the heavy cable-tool assembly could get jammed in the borehole and could no longer be repeatedly lifted and dropped. In the foreground of the photograph below, the large wheel at right (with small, square hub) received the uppermost part of a fishing pole. A rope was wound around this wheel’s rim and led to the “bull wheel” shaft.
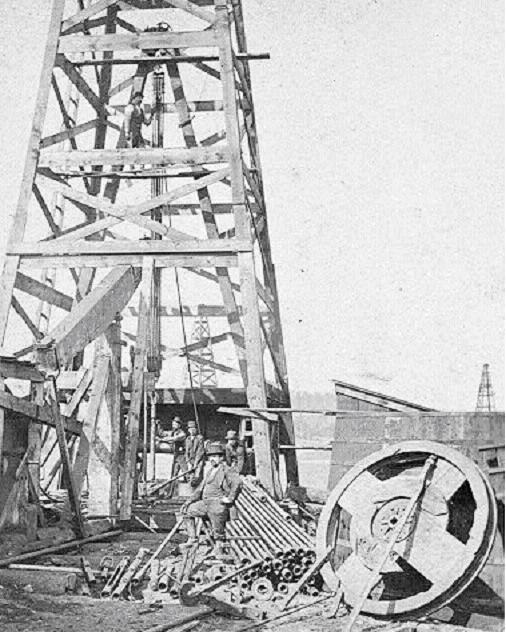
The term fishing came from early percussion drilling using cable tools. When the derrick’s manila rope or wire-line rope broke, a crewman lowered a hook and attempted to pull out the well’s heavy iron bit. Photo courtesy Library of Congress.
Among the fishing tools at the man’s feet are 3.5-inch iron poles, each 20 feet in length and weighing 500 pounds. To fish for stuck tools, these were lowered in well, armed at their end with a “die” with a left-hand thread cut in it. This die fit over the end of the stuck tool, tapered inward slightly, and when turned to the left, cut a thread on the cable tool.

The bull wheel, driven by the well’s steam-powered drilling engine, exerted a tremendous strain on the assembled poles. Since that strain was always to the left, the die gradually cut a thread in the stuck cable tool. One of the cable tool sections would eventually “yield, unscrew, and be removed.”
The operation repeated until the lowest piece was reached. A “spud” was then employed. Drilling usually would continue into the night, illuminated by two-wicked “yellow dog” lanterns.
Knives and Whipstocks
“Well fishing tools are constantly being improved and new ones introduced,” explained David T. Day in his A Handbook of the Petroleum Industry in 1922. Describing cable tool operations, he explained that the basic principle of well fishing tools often involved milled wedges — on a spear or in a cylinder — for recovering lost tubing or casing.
As drillers gained experience with deeper wells, patent applications included hundreds of designs for catching some tool or part that had been broken or lost in the borehole. Many of these “fishing tools” could be created on-site since most cable-tool rigs already had a forge for sharpening bits on the derrick floor.
Day noted that the simpler types of fishing tools comprised “horn sockets, corrugated friction sockets, rope grabs, rope spears, bit hooks, spuds, whipstocks, fluted wedges, rasps, bell sockets, rope knives, boot jacks, casing knives and die nipples.”
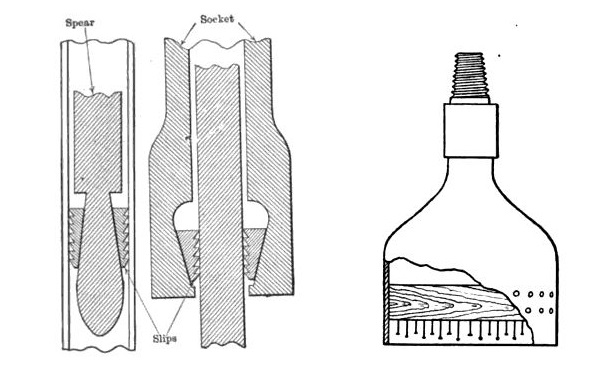
Basic fishing tools include the spear and socket, each with milled edges. Using nails and wax, an impression block helps determine what is stuck downhole. Image from A Handbook of the Petroleum Industry, 1922.
These and other devices, when used with an auger stem in various combinations called jars, can secure a powerful upward stroke or “jar” and thus dislodge and recover the tool being sought, Day explained in his 1922 book.
“The jars, essentially and universally used in fishing with cable tools, consist off two heavy forged-steel links, interlocking as the links of a cable chain, but fitting together more snugly,” he added.

“Many lost tools that cannot be recovered are drilled up or ‘side-tracked” (driven into or against the wall) and passed in drilling,” Day explained. Much depended upon “the skill and patience of the driller.”
Once all well fishing tools failed, a final resort was a whipstock, which allowed the bit to angle off and bypass the fish to leave the operator with a deviated hole. This was sometimes unpopular where wells were closely spaced.
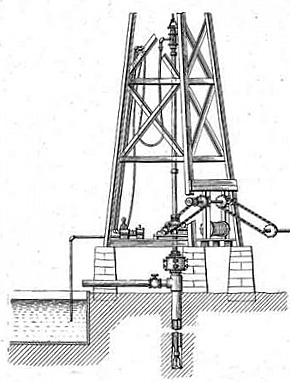
By the early 1900s, rotary drilling introduced the hollow drill stem that enabled broken rock debris to be washed out of the borehole. It led to far deeper wells.
As drilling with rotary rigs became more common in the early 1900s, fishing methods adapted. “In rotary drilling, the only tools ordinarily used in the well are the drill pipe and bits,” Day noted, adding that the rotary fishing tools, “were comparatively free from the complexities of cable-tool work.”
Most rotary fishing jobs were caused by “twist offs” (broken drill pipe), although the bit, drill coupling or tool joints may break or unscrew. As in cable-tool fishing, an impression block often was needed to determine the proper fishing tool.
But even back then — and especially now with wells miles deep and often turned horizontally — when a downhole problem occurred, the well could be lost for good.
Elk City, Deep Gas Capital
The Anadarko Basin extends across western Oklahoma into the Texas Panhandle and into southwestern Kansas and southeastern Colorado. It includes the Hugoton-Panhandle field, the Union City field and the Elk City field and is among the most prolific natural gas-producing areas in North America.
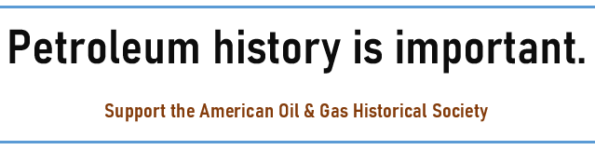
In 1980, the Oklahoma Historical Society and Oklahoma Petroleum Council dedicated a granite monument at Third and Pioneer streets in Elk City, Oklahoma. The Washita County marker notes:
The Deep Anadarko Basin of Western Oklahoma is one of the most prolific gas provinces of North America. Wells drilled here have been among the world’s deepest. The Bertha Rogers No. 1 in Washita County, drilled in 1971 to 31,441 feet, was then the world’s deepest well. In 1979 the No. 1 Sanders well near Sayre became Oklahoma’s deepest gas producer at 24,996 feet.
When controls on gas prices were lifted, Anadarko justified the faith and perseverance of The GHK Company and other operators who pioneered in deep drilling. The shallow horizons of Greater Anadarko account for much of this nation’s proved gas reserves. Deeper sediments below 15,000 feet remain virtually unexplored. Renewed assessment of some 22,000 cubic miles of deep sediments may carry over into the 21st Century.
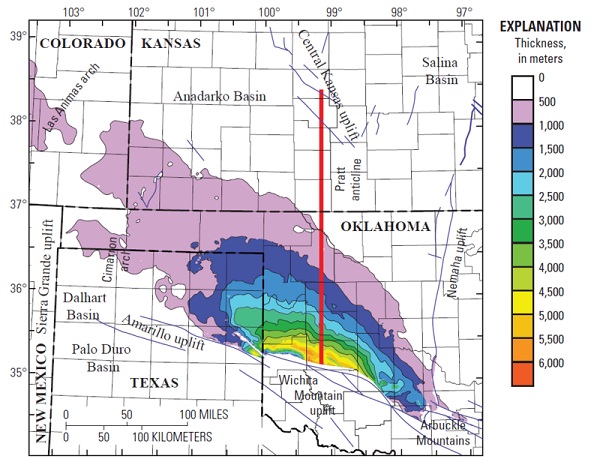
A 2014 geologic map of 50,000 square mile Anadarko Basin showing thickness of strata courtesy U.S. Geological Survey.
For the 20th century’s final quarter, the Basin remains the frontier of deep drilling technology centered on Elk City, “Deep Gas Capital of the World”. As gas prices equate more closely to value, the nation’s needs may be met increasingly from this massive sedimentary basin, a focal point in drilling innovation and geological interpretation.
In re-energizing America, Anadarko will not yield its gas easily or briefly. Promised rewards lying beyond the threshold of drilling techniques demand massive investment. In challenging the inventive enterprise of America’s energy industry, this Basin will remain the heartland of technology in penetrating the earth’s crust.
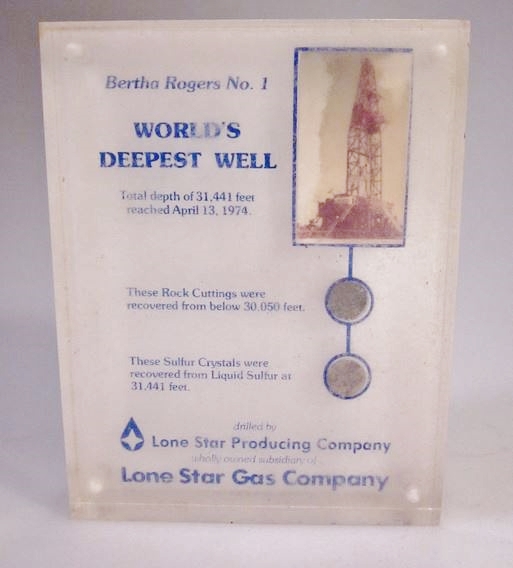
A 1974 souvenir of the Bertha Roger No. 1 well, which sought natural gas almost six miles deep in Oklahoma’s Anadarko Basin.
Until the 1960s, few companies could risk millions of dollars and push rotary rig drilling technology to reach beyond the 13,000-foot level in what geologists called “the deep gas play.”
The great expense and technological expertise necessary to complete ultra-deep natural gas wells at these depths made the Anadarko Basin “the domain of the major petroleum corporations,” explained Bobby Weaver, oil historian and frequent article contributor to the Oklahoma Historical Society.

GHK Company and partner Lone Star Producing Company believed ultra-deep wells in Oklahoma’s Anadarko Basin could produce massive amounts of natural gas. They began drilling wells more than three miles deep in the late 1960s.
South of Burns Flat in Washita County, their Bertha Rogers No.1 would reach almost six miles deep in 1974 — after a deep fishing trip.
Deep Fishing in Oklahoma
In March 1974 in far western Oklahoma, after 16 months of drilling and almost six miles deep, the Bertha Rogers No. 1 rotary rig drill stem sheared, leaving 4,111 feet of pipe and the drill bit stuck downhole. Spudded in November 1972 and averaging about 60 feet per day, the Bertha Rogers had been heading for the history books as the world’s deepest well at the time.
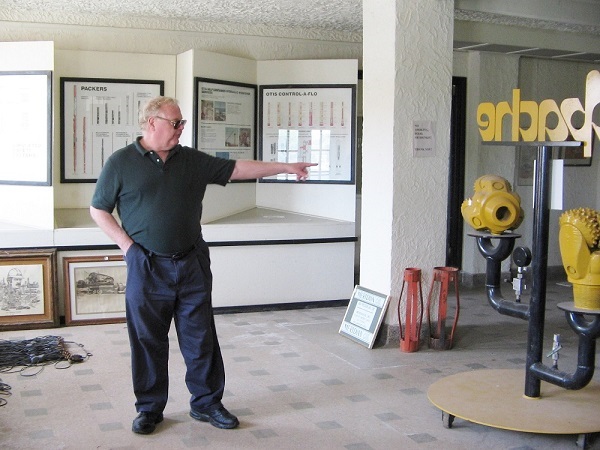
Independent producer John West in 2006 preserved artifacts in the closed Anadarko Basin Museum of Natural History in Elk City, Oklahoma. Photo by Bruce Wells.
It was March 1974 and the enormous investment of Lone Star Producing Company of Dallas, and partner GHK Company of Oklahoma City, was about to be lost. Desperate GHK executives turned to a “fishing” company in Texas.
Millions of dollars hung in the balance when Houston-based Wilson Downhole Service Company, was called and tool-fishing expert Mack Ponder sent to the rescue.
Against all odds and employing the latest 1970s technology, Ponder was able to retrieve the pipe sections and drill bit from 30,019 feet down, bringing operations back online and enabling drilling to continue even deeper into Oklahoma’s Anadarko Basin, at a site about 12 miles west of Cordell.
Although the remarkable deep fishing achievement was celebrated, the Bertha Rogers No. 1 had to be completed at just 14,000 feet after striking molten sulfur at 31,441 feet. The equipment could not take the abuse at total depth. The well set a world record and remains one of the deepest ever drilled.
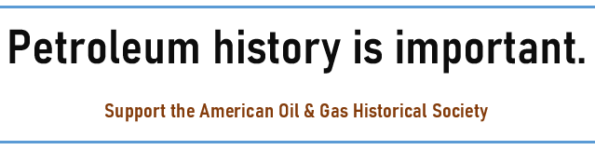
Completed at a depth of almost 25,000 feet, the Beckham County well would become Oklahoma’s deepest natural gas producer (also see Anadarko Basin in Depth`).
Oil Well Fishing Tool Technician
The U.S. Labor Department describes an “Oil Well Fishing Tool Technician” (Occupational Title 930.261-010) as an occupation that “analyzes conditions of unserviceable oil or gas wells and directs use of special well-fishing tools and techniques to recover lost equipment and other obstacles from boreholes of wells,”
The government description adds that the technician plans fishing methods, selects tools, and “directs drilling crew in applying weights to drill pipes, in using special tools, in applying pressure to circulating fluid (mud), and in drilling around lodged obstacles or specified earth formations, using whipstocks and other special tools.”
_______________________
Recommended Reading: History Of Oil Well Drilling
(2007); The Prize: The Epic Quest for Oil, Money & Power (1991); The Extraction State, A History of Natural Gas in America (2021). Your Amazon purchase benefits the American Oil & Gas Historical Society. As an Amazon Associate, AOGHS earns a commission from qualifying purchases.
_______________________
The American Oil & Gas Historical Society (AOGHS) preserves U.S. petroleum history. Please become an AOGHS supporter and help maintain this energy education website and expand historical research. For more information, contact bawells@aoghs.org. Copyright © 2024 Bruce A. Wells. All rights reserved.
Citation Information – Article Title: “Fishing in Petroleum Wells.” Authors: B.A. Wells and K.L. Wells. Website Name: American Oil & Gas Historical Society. URL: https://aoghs.org/petroleum-art/high-flying-trademark. Last Updated: December 28, 2024. Original Published Date: June 1, 2006.
by Bruce Wells | Dec 28, 2024 | Petroleum Technology
Early patent for a hollow “drill-rod” and roller bit for “making holes in hard rock.”
An “Improvement in Rock Drills” patent issued to a New Yorker after the Civil War included the basic elements of the modern petroleum industry’s rotary rig.
On January 2, 1866, Peter Sweeney of New York City was granted U.S. patent No. 51,902 for a drilling system with many innovative technologies. His rotary rig design, which improved upon an 1844 British patent by Robert Beart, applied the rotary drilling method’s “peculiar construction particularly adapted for boring deep wells.”
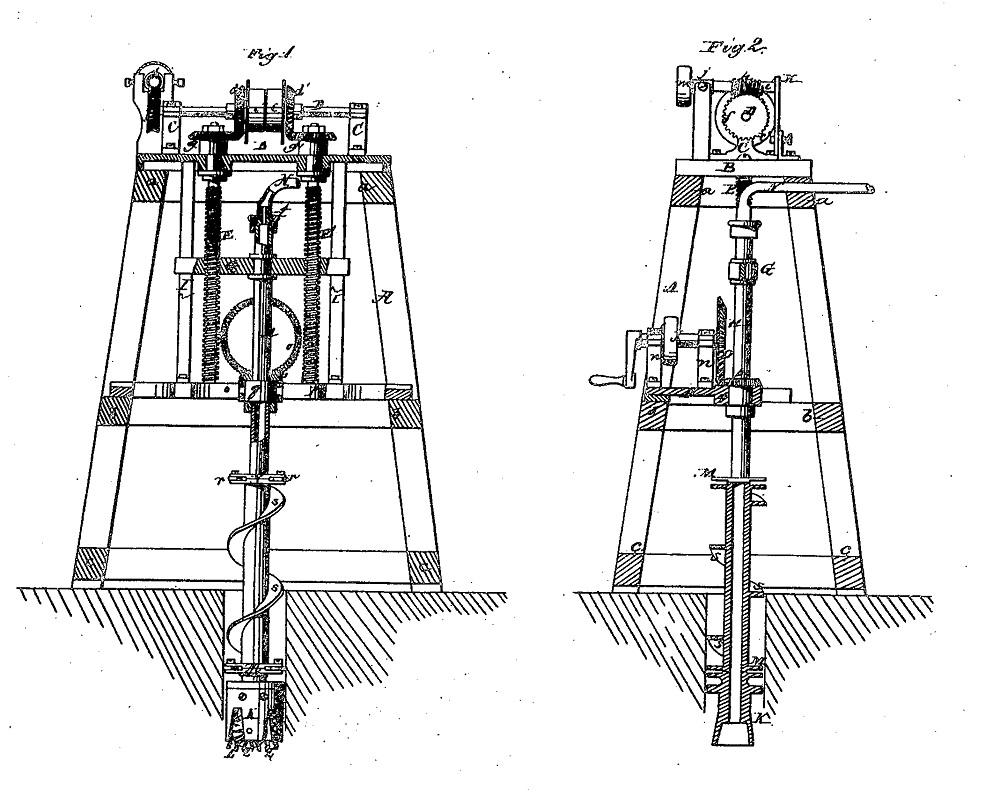
Peter Sweeney’s innovative 1866 “Stone Drill” patent included a roller bit using a “rapid rotary motion” that would evolve into modern rotary drilling technologies.
More efficient than traditional cable-tool percussion bits, Sweeney’s patent provided for a roller bit with replaceable cutting wheels such “that by giving the head a rapid rotary motion the wheels cut into the ground or rock and a clean hole is produced.”
Deeper Drilling
The Sweeney design utilized a roller bit with replaceable cutting wheels such “that by giving the head a rapid rotary motion the wheels cut into the ground or rock and a clean hole is produced.
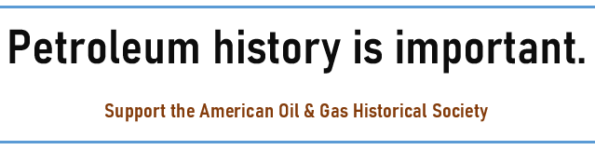
In another innovation, the “drill-rod” was hollow and connected with a hose through which “a current of steam or water can be introduced in such a manner that the discharge of the dirt and dust from the bottom of the hole is facilitated.”
Better than commonly used steam-powered cable-tools, which used heavy rope to lift and drop iron chisel-like bits, Sweeney claimed his drilling apparatus could be used with great advantage for “making holes in hard rock in a horizontal, oblique, or vertical direction.”
Drilling operations could be continued without interruption, Sweeny explained in his patent application, “with the exception of the time required for adding new sections to the drill rod as the depth of the hole increases. The dirt is discharged during the operation of boring and a clean hole is obtained into which the tubing can be introduced without difficulty.”
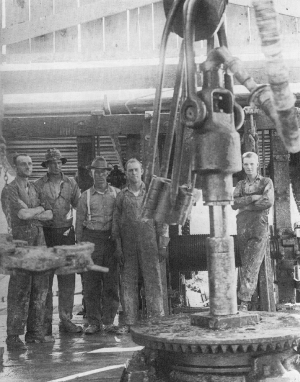
A 1917 rotary rig in the Coalinga, California, oilfield. Courtesy of the Joaquin Valley Geology Organization.
Foreseeing the offshore exploration industry, Sweeney’s patent concluded with a note that “the apparatus can also be used with advantage for submarine operations.”

With the U.S. oil industry’s growth after the first commercial well in 1859, drilling contractors quickly improved upon Sweeney’s idea. A device was fitted to the rotary table that clamped around the drill pipe and turned. As this “kelly bushing” rotated, the pipe rotated and with it the bit downhole. The torque of the rotary table was transmitted to the drill stem.
Thirty-five years after Sweeney’s patent, rotary drilling revolutionized the petroleum industry after a 1901 oil discovery by Capt. Anthony Lucas launched a drilling boom at Spindletop Hill in Texas.
Learn more at Making Hole – Drilling Technology.
_______________________
Recommended Reading: History Of Oil Well Drilling
(2007); The Prize: The Epic Quest for Oil, Money & Power (1991); The Extraction State, A History of Natural Gas in America (2021). Your Amazon purchase benefits the American Oil & Gas Historical Society. As an Amazon Associate, AOGHS earns a commission from qualifying purchases.
_______________________
The American Oil & Gas Historical Society (AOGHS) preserves U.S. petroleum history. Please become an AOGHS annual supporter and help maintain this energy education website and expand historical research. For more information, contact bawells@aoghs.org. Copyright © 2024 Bruce A. Wells. All rights reserved.
Citation Information – Article Title: “Sweeney’s 1866 Rotary Rig.” Authors: B.A. Wells and K.L. Wells. Website Name: American Oil & Gas Historical Society. URL: https://aoghs.org/technology/1866-patent-rotary-rig. Last Updated: December 27, 2024. Original Published Date: January 2, 2013.
by Bruce Wells | Dec 13, 2024 | Petroleum Technology
“Small cannons throwing a three-inch solid shot are kept at various stations throughout the region…”
Early petroleum technologies included cannons for fighting oil tank storage fires, especially in the Great Plains where lightning strikes ignited derricks, engine houses and tanks. Shooting a cannon ball into the base of a burning storage tank allowed oil to drain into a holding pit or ditch, putting out the fire.
“Oil Fires, like battles, are fought by artillery,” proclaimed the Massachusetts Institute of Technology in December 1884. Oilfield conflagrations had challenged America’s petroleum industry since the first commercial well in 1859 (see First Oil Well Fire). An MIT student offered a recent, first-person account.
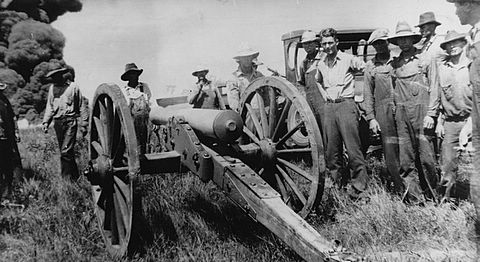
Especially in mid-west oilfields, lightning strikes could ignite derricks, engine houses, and rows of storage tanks. Photo courtesy Butler County History Center & Kansas Oil Museum.
“Lightning had struck the derrick, followed pipe connections into a nearby tank and ignited natural gas, which rises from freshly produced oil. Immediately following this blinding flash, the black smoke began to roll out,” the writer noted in The Tech, a student newspaper established in 1881.
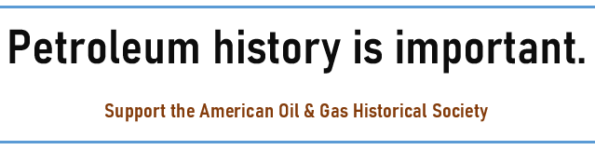
The MIT article, “A Thunder Storm in the Oil Country,” described what happened next:
“Without stopping to watch the burning tank-house and derrick, we followed the oil to see where it would go. By some mischance the mouth of the ravine had been blocked up and the stream turned abruptly and spread out over the alluvial plain,” reported the article.
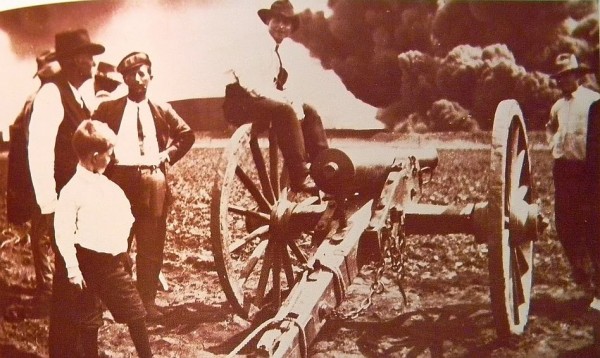
Oilfield operators used muzzle-loading cannons to fired solid shot at the base of burning oil tanks, draining the oil into ditches to extinguish the blaze.
“Here, on a large smooth farm, were six iron storage tanks, about 80 feet in diameter and 25 feet high, each holding 30,000 barrels of oil,” it added, noting the burning oil “spread with fearful rapidity over the level surface” before reaching an oil storage tank.
“Suddenly, with loud explosion, the heavy plank and iron cover of the tank was thrown into the air, and thick smoke rolled out,” the writer observed.
“Already the news of the fire had been telegraphed to the central office and all its available men and teams in the neighborhood ordered to the scene,” he added. “The tanks, now heated on the outside as well as inside, foamed and bubbled like an enormous retort, every ejection only serving to increase the heat.”
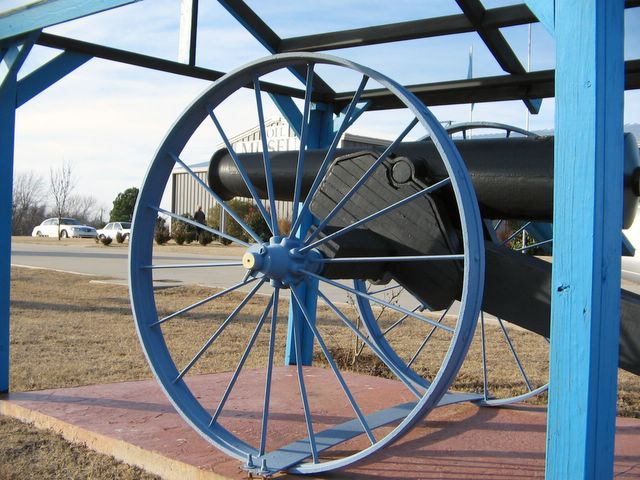
Technological innovations in Oklahoma oilfields helped improve petroleum production worldwide. The oilfield artillery exhibit at the Oklahoma Oil Museum in Seminole educated visitors until the museum closed in 2019. Photo by Bruce Wells.
The area of the fire rapidly extended to two more tanks: “These tanks, surrounded by fire, in turn boiled and foamed, and the heat, even at a distance, was so intense that the workmen could not approach near enough to dig ditches between the remaining tanks and the fire.”

Noting the arrival of “the long looked for cannon,” the reporter noted, adding, “since the great destruction is caused by the oil becoming overheated, foaming and being projected to a distance, it is usually desirable to let it out of the tank to burn on the ground in thin layers; so small cannons throwing a three-inch solid shot are kept at various stations throughout the region for this purpose.”
The wheeled cannon was placed in position and “aimed at points below the supposed level of the oil and fired,” explained the witness. “The marksmanship at first was not very good, and as many shots glanced off the iron plates as penetrated, but after a while nearly every report was followed by an outburst.”
The oil in three storage tanks was slowly drawn down by this means, “and did not again foam over the top, and the supply to the river being thus cut off the fire then soon died away.”
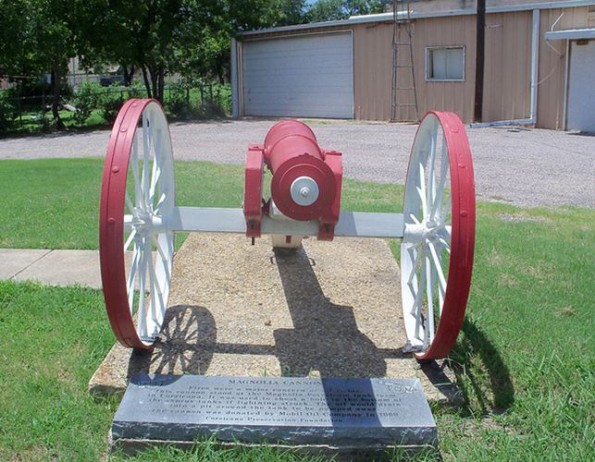
A cannon from the Magnolia Petroleum tank farm was donated to the city of Corsicana, Texas, by Mobil Oil Company in 1969.
In the end, “it was not till the sixth day from that on which we saw the first tank ignited that the columns of flame and smoke disappeared. During this time 180,000 barrels of crude oil had been consumed, besides the six tanks, costing $10,000 each, destroyed,” concluded the 1884 MIT article.
Visitors to Corsicana, Texas — where oil was discovered while drilling for water in 1894 (see First Texas Oil Boom) — can view an oilfield cannon donated to the city in 1969 by Mobil Oil. The marker notes:
“Fires were a major concern of oil fields. This cannon stood at the Magnolia Petroleum tank farm in Corsicana. It was used to shoot a hole in the bottom of the Cyprus tanks if lightning struck. The oil would drain into a pit around the tank to be pumped away. The cannon was donated by Mobil Oil Company in 1969.”
Another cannon can be found on exhibit in Bartlesville, Oklahoma, near the first Oklahoma oil well, drilled a decade before 1907 statehood. Exhibits at Discovery One Park include an 84-foot cable-tool derrick first erected in 1948 and replaced in 2008.

Oilfield artillery also can be found at the Kansas Oil Museum in Butler County.
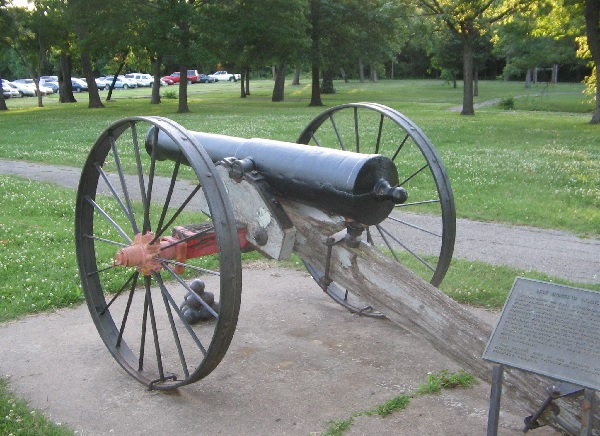
An oilfield cannon exhibit in Discovery One Park, the Bartlesville site of the first significant Oklahoma oilfield discovery of 1897. Photo by Bruce Wells.
Another educated tourists in Ohio. The Wood County Historical Center and Museum in Bowling Green displays its own “unusual fire extinguisher” among its collection. The Buckeye Pipeline Company of Norwood donated the cannon, according to the museum’s Kelli King.
“The cannon, cast in North Baltimore (Ohio), was used in the 1920s in Cygnet before being moved to Northwood,” Kelli says, adding that more local history can be found in the museum’s documentary “Ohio Crude” and in its exhibit, “Wood County in Motion.” Museums in nearby Hancock County and Allen County also have interesting petroleum collections.
Modern Oilfield Fire Fighting
When oilfield well control expert and firefighter Paul “Red” Adair died at age 89 in 2004, he left behind a famous “Hell Fighter” legacy. The son of a blacksmith, Adair was born in 1915 in Houston and served with a U.S. Army bomb disposal unit during World War II.
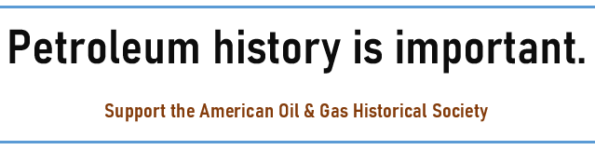
Adair began his career working for Myron M. Kinley, who patented a technology for using charges of high explosives to snuff out well fires. Kinley, whose father had been an oil well shooter in California in the early 1900s, also mentored Asger “Boots” Hansen and “Coots” Mathews of Boots & Coots International Well Control and other firefighters.

Famed oilfield firefighter Paul “Red” Adair of Houston, Texas, in 1964.
In 1959, Adair founded Red Adair Company in Houston and soon developed innovative techniques for “wild well” control. His company would put out more than 2,000 well fires and blowouts worldwide — onshore and offshore.
The Texas firefighter’s skills were tested in 1991 when Adair and his company extinguished 117 oil well fires set in Kuwait by Saddam Hussein’s retreating Iraqi army. Adair was joined by other pioneering well firefighting companies, including Cudd Well Control, founded by Bobby Joe Cudd in 1977.
Russian Anti-Tank Gun
Unable to control a 2020 oil well fire in Siberia, a Russian oil company called in the army. In May, a well operated by the Irkutsk Oil Company in Russia’s Irkutsk region ignited into a geyser of flame. When Irkutsk Oil Company firefighters were unable to extinguish the blaze, the Russian Defense Ministry flew a Rapira MT-12 an anti-tank gun to the well site.
The Russian army’s 100-millimeter gun repeatedly fired at the flaming wellhead, “breaking it from the well and allowing crews to seal the well,” according to a June 8, 2020, article in Popular Mechanics.
In 1966, the Soviet Union used a nuclear device to extinguish a natural gas fire — as U.S. scientists experimented with nuclear fracturing of natural gas wells (see Project Gasbuggy tests Nuclear “Fracking”).

Learn more about the earliest oilfield fires and how the petroleum industry fought them with cannons, wind-making machines (including jet engines), and nuclear bombs in Oilfield Firefighting Technologies.
_______________________
Recommended Reading: Trek of the Oil Finders: A History of Exploration for Petroleum (1975); The Prize: The Epic Quest for Oil, Money & Power (1991); Myth, Legend, Reality: Edwin Laurentine Drake and the Early Oil Industry
(2009). Your Amazon purchase benefits the American Oil & Gas Historical Society. As an Amazon Associate, AOGHS earns a commission from qualifying purchases.
_______________________
The American Oil & Gas Historical Society (AOGHS) preserves U.S. petroleum history. Please become an AOGHS annual supporter and help maintain this energy education website and expand historical research. For more information, contact bawells@aoghs.org. Copyright © 2024 Bruce A. Wells. All rights reserved.
Citation Information – Article Title: “Oilfield Artillery fights Fires.” Authors: B.A. Wells and K.L. Wells. Website Name: American Oil & Gas Historical Society. URL: https://aoghs.org/technology/oilfield-artillery-fights-fires. Last Updated: December 12, 2024. Original Published Date: September 1, 2005.
by Bruce Wells | Dec 5, 2024 | Petroleum Technology
Government scientists experimented with atomic blasts to fracture natural gas wells.
Project Gasbuggy was the first in a series of Atomic Energy Commission downhole nuclear detonations to release natural gas trapped in shale. This was “fracking” late 1960s style.
In December 1967, government scientists — exploring the peacetime use of controlled atomic explosions — detonated Gasbuggy, a 29-kiloton nuclear device they had lowered into an experimental well in rural New Mexico. The Hiroshima bomb of 1945 was about 15 kilotons.
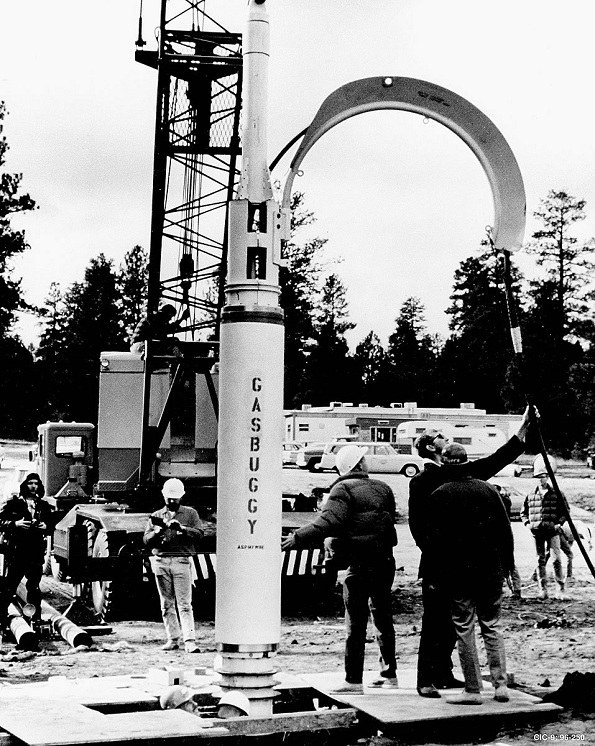
Scientists lowered a 13-foot by 18-inch diameter nuclear device into a New Mexico gas well. The experimental 29-kiloton Project Gasbuggy bomb was detonated at a depth of 4,240 feet. Photo courtesy Los Alamos Lab.
The Project Gasbuggy team included experts from the Atomic Energy Commission, the U.S. Bureau of Mines, and El Paso Natural Gas Company. They sought a new, powerful method for fracturing petroleum-bearing formations.
Near three low-production natural gas wells, the team drilled to a depth of 4,240 feet — and lowered a 13-foot-long by 18-inch-wide nuclear device into the borehole.
Plowshare Program: Peaceful Nukes
The 1967 experimental explosion in New Mexico was part of a wider set of experiments known as Plowshare, a program established by the Atomic Energy Commission in 1957 to explore the constructive use of nuclear explosive devices.
“The reasoning was that the relatively inexpensive energy available from nuclear explosions could prove useful for a wide variety of peaceful purposes,” noted a report later prepared for the U.S. Department of Energy.
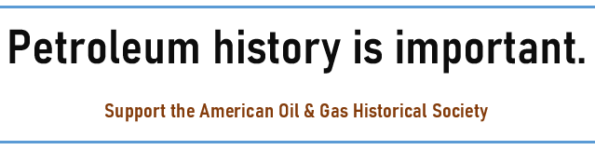
From 1961 to 1973, researchers carried out dozens of separate experiments under the Plowshare program — setting off 29 nuclear detonations. Most of the experiments focused on creating craters and canals. Among other goals, it was hoped the Panama Canal could be inexpensively widened.”
In the end, although less dramatic than nuclear excavation, the most promising use for nuclear explosions proved to be for stimulation of natural gas production,” explained the September 2011 government report.
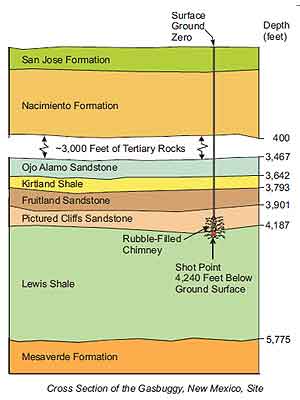
Detonated 60 miles from Farmington in 1967, the first nuclear detonation created a “Rubble Filled Chimney,” producing 295 million cubic feet of natural gas — and deadly Tritium radiation.
Tests, mostly conducted in Nevada, also took place in the petroleum fields of New Mexico and Colorado. Project Gasbuggy was the first of three nuclear fracturing experiments that focused on stimulating natural gas production. Two later tests took place in Colorado.
Atomic Energy Commission scientists worked with experts from the Astral Oil Company of Houston, with engineering support from CER Geonuclear Corporation of Las Vegas.
The experimental wells, which required custom drill bits to meet the hole diameter and narrow hole deviation requirements, were drilled by Denver-based Signal Drilling Company or its affiliate, Superior Drilling Company.
Projects Rulison and Rio Blanco
In 1969, Project Rulison, the second of the three nuclear well stimulation projects, blasted a natural gas well near Rulison, Colorado. Scientists detonated a 43-kiloton nuclear device almost 8,500 feet underground to produce commercially viable amounts of natural gas.
In 1973, another fracturing experiment at Rio Blanco, northwest of Rifle, Colorado, was designed to increase natural gas production from low-permeability sandstone.
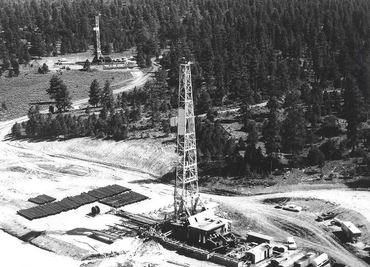
Gasbuggy: “Site of the first United States underground nuclear experiment for the stimulation of low-productivity gas reservoirs.” Photo Courtesy DOE.
The May 1973 Rio Blanco test consisted of the nearly simultaneous detonation of three 33-kiloton devices in a single well, according to the Office of Environmental Management. The explosions occurred at depths of 5,838, 6,230, and 6,689 feet below ground level. It would prove to be the last experiment of the Plowshare program.
Although a 50-kiloton nuclear explosion to fracture deep oil shale deposits — Project Bronco — was proposed, it never took place. Growing knowledge (and concern) about radioactivity ended these tests for the peaceful use of nuclear explosions. The Plowshare program was canceled in 1975.

After an examination of all the nuclear test projects, the U.S. Department of Energy September 2011 reported:
By 1974, approximately 82 million dollars had been invested in the nuclear gas stimulation technology program (i.e., nuclear tests Gasbuggy, Rulison, and Rio Blanco). It was estimated that even after 25 years of gas production of all the natural gas deemed recoverable, only 15 to 40 percent of the investment could be recovered. At the same time, alternative, non-nuclear technologies were being developed, such as hydrofracturing.
DOE concluded, Consequently, under the pressure of economic and environmental concerns, the Plowshare Program was discontinued at the end of FY 1975.
Project Gasbuggy: Nuclear Fracking
“There was no mushroom cloud, but on December 10, 1967, a nuclear bomb exploded less than 60 miles from Farmington,” explained historian Wade Nelson in an article written three decades later, “Nuclear explosion shook Farmington.”
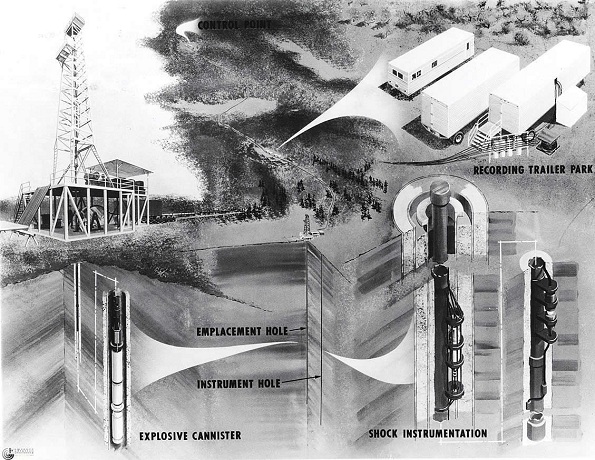
Government scientists believed a nuclear device would provide “a bigger bang for the buck than nitroglycerin” for fracturing dense shales and releasing natural gas. Illustration courtesy Los Alamos Lab.
The 4,042-foot-deep detonation created a molten glass-lined cavern about 160 feet in diameter and 333 feet tall. It collapsed within seconds. Subsequent measurements indicated fractures extended more than 200 feet in all directions — and significantly increased natural gas production.
A September 1967 Popular Mechanics article described how nuclear explosives could improve previous fracturing technologies, including gunpowder, dynamite, TNT — and fractures “made by forcing down liquids at high pressure.”
Hydraulic fracturing technologies pump a mixture of fluid and sand down a well at extremely high pressure to stimulate production of oil and natural gas wells.
The first commercial application of hydraulic fracturing took place in March 1949 near Duncan, Oklahoma, following experiments in a Kansas natural gas field. Increasing oil production by fracturing geologic formations had begun about a century earlier (see Shooters – A “Fracking” History).
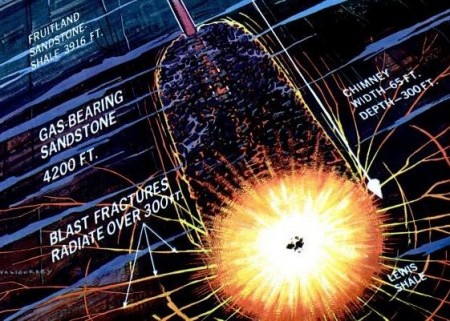
A 1967 illustration in Popular Mechanics magazine showed how a nuclear explosive would improve earlier technologies by creating bigger fractures and a “huge cavity that will serve as a reservoir for the natural gas.”
Scientists predicted that nuclear explosives would create more and bigger fractures “and hollow out a huge cavity that will serve as a reservoir for the natural gas” released from the fractures.

“Geologists had discovered years before that setting off explosives at the bottom of a well would shatter the surrounding rock and could stimulate the flow of oil and gas,” Nelson explained. “It was believed a nuclear device would simply provide a bigger bang for the buck than nitroglycerin, up to 3,500 quarts of which would be used in a single shot.”
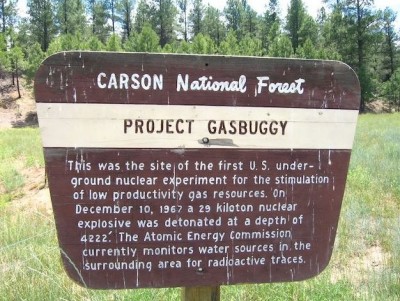
The first 1967 underground detonation test was part of a broader federal program begun in the late 1950s to explore the peaceful uses of nuclear explosions.
“Today, all that remains at the site is a plaque warning against excavation and perhaps a trace of tritium in your milk,” Nelson added in his 1999 article. He quoted James Holcomb, the site foreman for El Paso Natural Gas, who saw a pair of white vans that delivered pieces of the disassembled nuclear bomb.
“They put the pieces inside this lead box, this big lead box…I (had) shot a lot of wells with nitroglycerin and I thought, ‘That’s not going to do anything,” reported Holcomb. A series of three production tests, each lasting 30 days, was completed during the first half of 1969. Government records indicated the Gasbuggy well produced 295 million cubic feet of natural gas.
“Nuclear Energy: Good Start for Gasbuggy,” proclaimed the December 22, 1967, TIME magazine. The Department of Energy, which had hoped for much higher production, determined that Tritium radiation contaminated the gas. It flared — burned off — the gas during production tests that lasted until 1973. Tritium is a naturally occurring radioactive form of hydrogen.
A 2012 Nuclear Regulatory Commission report noted, “Tritium emits a weak form of radiation, a low-energy beta particle similar to an electron. The tritium radiation does not travel very far in air and cannot penetrate the skin.”
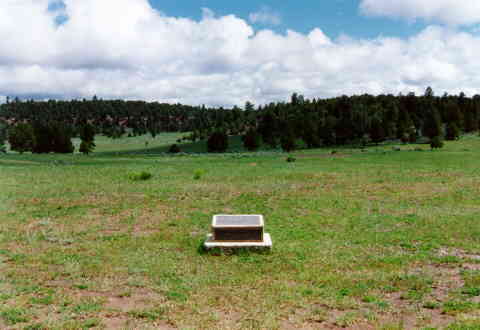
A plaque marks the site of Project Gasbuggy in the Carson National Forest, 90 miles northwest of Santa Fe, New Mexico.
According to Nelson, radioactive contamination from the flaring “was minuscule compared to the fallout produced by atmospheric weapons tests in the early 1960s.” From the well site, Holcomb called the test a success. “The well produced more gas in the year after the shot than it had in all of the seven years prior,” he said.
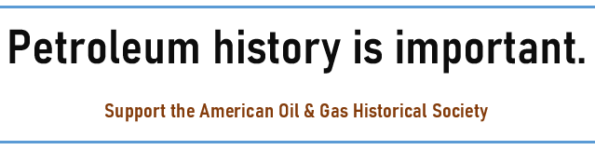
In 2008, the Energy Department’s Office of Legacy Management assumed responsibility for long-term surveillance and maintenance at the Gasbuggy site. A marker placed at the Gasbuggy site by the Department of Energy in November 1978 reads:
Site of the first United States underground nuclear experiment for the stimulation of low-productivity gas reservoirs. A 29 kiloton nuclear explosive was detonated at a depth of 4227 feet below this surface location on December 10, 1967. No excavation, drilling, and/or removal of materials to a true vertical depth of 1500 feet is permitted within a radius of 100 feet of this surface location. Nor any similar excavation, drilling, and/or removal of subsurface materials between the true vertical depth of 1500 feet to 4500 feet is permitted within a 600 foot radius of t 29 n. R 4 w. New Mexico principal meridian, Rio Arriba County, New Mexico without U.S. Government permission.
USSR’s Project NEVA
The Union of Soviet Socialist Republics (USSR) responded with its own more extensive program in 1965, according to a declassified 1981 Central Intelligence Agency report.
The CIA assessment, “The Soviet Program for Peaceful Uses of Nuclear Explosions,” reported that by the mid-1970s, the Soviets had detonated nine nuclear devices in seven Siberian fields to increase natural gas production as part of Project NEVA – Nuclear Explosions for the National Economy.
The USSR atomic tests delivered essentially the same conclusion as did America’s Project Gasbuggy – no commercially feasible petroleum production — and not popular with the public because of environmental concerns. The USSR abandoned Project NEVA experiments in 1989, more than a decade after the end of America’s Plowshare program.
Parker Drilling Rig No. 114
In 1969, Parker Drilling Company signed a contract with the U.S. Atomic Energy Commission to drill a series of holes up to 120 inches in diameter and 6,500 feet in depth in Alaska and Nevada for additional nuclear bomb tests. Parker Drilling’s Rig No. 114 was one of three special rigs built to drill the wells.
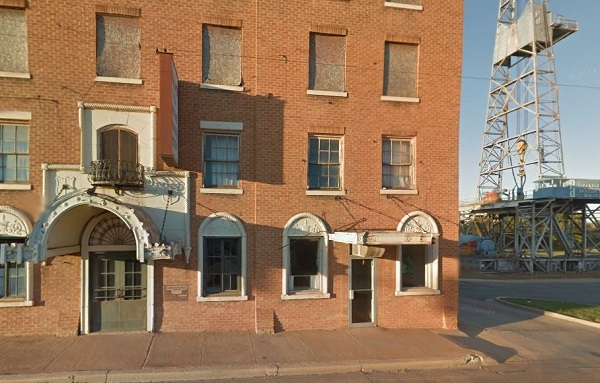
Parker Drilling Rig No. 114 was among those used to drill wells for nuclear detonations and later modified to drill conventional, very deep wells. Since 1991, the 17-story rig has welcomed visitors to Elk City, Oklahoma, next to the shuttered Anadarko Museum of Natural History. Photo by Bruce Wells.
Founded in Tulsa in 1934 by Gifford C. Parker, by the 1960s Parker Drilling had set numerous world records for deep and extended-reach drilling.
According to the Baker Library at the Harvard Business School, the company “created its own niche by developing new deep-drilling technology that has since become the industry standard.”

Following completion of the nuclear-test wells, Parker Drilling modified Rig No. 114 and its two sister rigs to drill conventional wells at record-breaking depths.
After retiring Rig No. 114 from oilfields, Parker Drilling in 1991 loaned it to Elk City, Oklahoma, as an energy education exhibit next to the Anadarko Museum of Natural History, which later closed. The 17-story rig has remained there to welcome Route 66 and I-40 travelers.
Learn about drilling miles deep in Anadarko Basin in Depth.
_______________________
Recommended Reading: Atoms for Peace and War 1953-1961
(2017); Project Plowshare: The Peaceful Use of Nuclear Explosives in Cold War America
(2012). Your Amazon purchase benefits the American Oil & Gas Historical Society. As an Amazon Associate, AOGHS earns a commission from qualifying purchases.
_______________________
The American Oil & Gas Historical Society (AOGHS) preserves U.S. petroleum history. Please become an AOGHS annual supporter and help maintain this energy education website and expand historical research. For more information, contact bawells@aoghs.org. Copyright © 2024 Bruce A. Wells. All rights reserved.
Citation Information – Article Title: “Project Gasbuggy tests Nuclear “Fracking”.” Authors: B.A. Wells and K.L. Wells. Website Name: American Oil & Gas Historical Society. URL: https://aoghs.org/technology/project-gasbuggy. Last Updated: December 4, 2024. Original Published Date: December 10, 2013.
by Bruce Wells | Nov 26, 2024 | Petroleum Technology
Scientists experiment with reflection seismography in 1921.
Exploring seismic waves is all about the vital earth science technology — reflection seismography — which revolutionized petroleum exploration in the 1920s. Seismic waves have led to oilfield discoveries worldwide and billions of barrels of oil.
(more…)